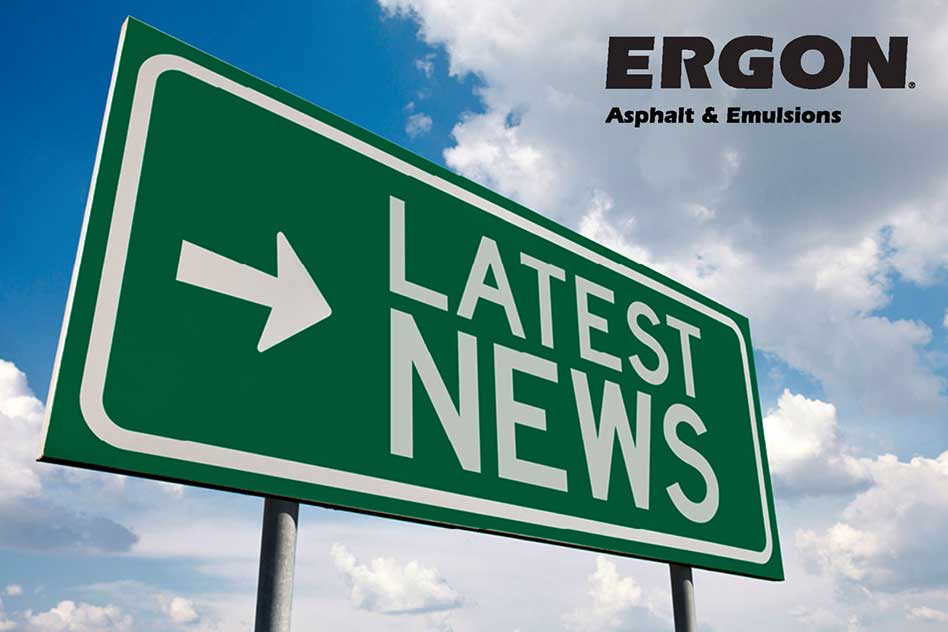
A little bit of Bainbridge is part of the new pavement project at Daytona International Speedway.
Ergon, a nine-employee plant on Spring Creek Road, is producing 82.5 tons of PG82-22, a special asphalt mix that is being used for the new repaving project at the Super Bowl of auto racing. The local manufacturer is also supplying 2,400 tons of another asphalt mix that doesn’t have the special characteristics that the PG82-22 has.
“We’re very proud. It’’s kind of a feather in our cap,” said Georgia Bedwell, the manager of the Bainbridge Ergon plant.
The special asphalt is a big part in repaving the 2.5-mile, 30-degree steep-banked track. Everything down to the historic track’s original limestone base is being removed and repaved. The special asphalt is being mixed with other components to comprise the new track.
According to NASCAR.com, the entire repaving project encompasses 1.4 million square feet, which will take approximately 50,000 tons of asphalt–not including the new concrete pit boxes.
“It’s a special mix we make for race tracks,“ Bedwell said. Although Ergon has produced the special formula for other race track repaving projects, such as Talladega’s, this is the first time the Bainbridge plant has produced the special mixture.
Ergon developed the special polymer mixer in 2008.
The liquid mixture is shipped from Bainbridge to Daytona at 360 to 380 degrees. The contractor, Lane Construction, then mixes the special formula with other elements to exact specifications in a mobile asphalt plant located in a parking lot behind Turn 2 of the speedway.
What’s so special about PG82-22?
It has memory.
A sample of the asphalt the length of a pencil can be stretched to more than 3 feet, than it would snap back to its original shape. That’s key when there are 3,500-pound cars traveling close to 200 mph on 30-degree banking.
“You can pull it and it goes back to its original form,” said Bedwell, who is scheduled to visit the race track and the paving project’s progress. “That’s why it’s so good on race tracks.”
But don’t expect Bedwell to be in awe of just being at the historic track during one of its more important renovation projects in recent history.
“I know who Jeff Gordon is and someone named Stewart,” Bedwell said, admitting that she doesn’t follow NASCAR much. She has been with Ergon for 27 years, but transferred to Bainbridge from the company’s Memphis, Tenn., terminal in 1993 when Ergon moved to Bainbridge.
The special asphalt is also supposed to minimize wear and tear on a track, and that memory could also prevent the track from forming any ruts or groves, Bedwell said.
Six tests are performed on the asphalt mix before it leaves Bainbridge.
Mitch Comerford, the lab technician with Ergon, knows the asphalt is ready for Daytona’s track when a black sample of the mixture, placed under a microscope, is actually all yellow. Unlike some asphalt that is used for other applications such as Department of Transportation projects on highways that has some specs of black in it, Comerford won’t give the OK for the mixture until he detects zero black specs.
If the mixture passes all its tests, it will not flow when it’s poured onto the track, but will be stationary once its cooled and formed.
During last February’s running of the Daytona 500, the race was stopped because the old pavement was coming up; the repaving project was started shortly after the finish of the track’s Fourth of July race. The project is expected to be completed in time for the next running of the Daytona 500.
Bedwell said the whole process using their special asphalt mixture has been thoroughly researched.
“This affects people’s lives,“ Bedwell said.