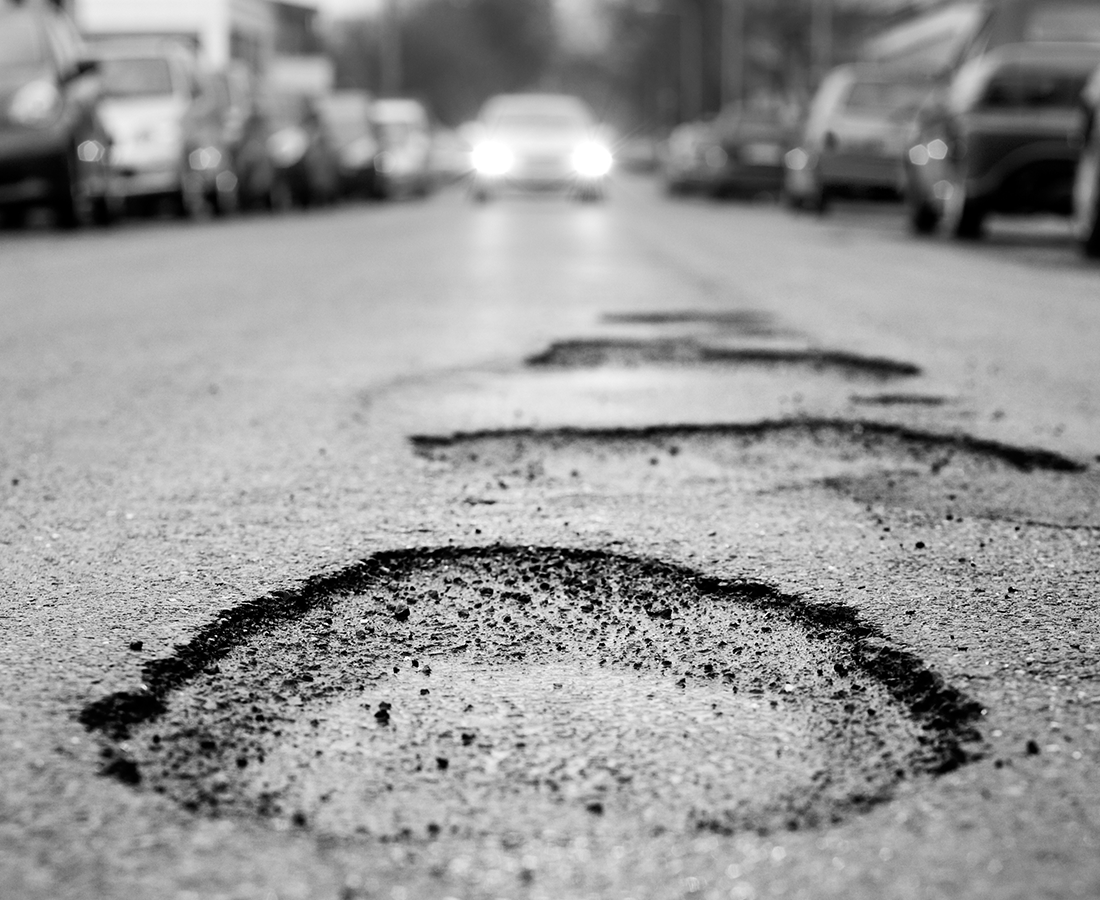
ePatch High-Performance Cold Mix Emulsion
Changing weather conditions from hot to cold combined with rain often lead to uneven road surfaces, edge deterioration and potholes. While it seems there are as many cold patch products as there are potholes, not all are created equal.
Ergon Asphalt & Emulsions’ revolutionary ePatch is a high-performance cold mix emulsion specifically designed to correct a variety of distresses and add stability to weakened pavement. Agency pavement preservation programs benefit from the use of ePatch to stabilize roads for years before more extensive treatments are required.
When road crews in Washington County, AR, needed an economical way to treat heavily damaged and potholed roads, they turned to ePatch. An increase in traffic during a particularly harsh and rainy winter had caused heavy damage to roadways, creating a safety concern and requiring an immediate call to action. ePatch provided a quick and cost-effective solution, stabilizing the roads for several years before more extensive treatments could be applied. Best of all, ePatch saved the County half the cost of other repair methods, allowing them to continue long-term planning for more extensive road projects.
Several factors play into the popularity and success of ePatch:
Variety of Production Options
Waiting on hot mix is not always ideal. In some instances, hot mix plants only run a few months out of the year. Some have no set schedule and run only when demand can justify operating the plant, or the mix they are running may not be suitable for patching potholes, leaving agencies with limited options.
With ePatch, contractors have the ability to self-supply by using Ergon A&E’s specially engineered emulsion and local aggregate (or even recycled aggregate in some cases) through a pugmill. The materials are churned into a mostly homogenous mixture which can then be transported directly to a worksite or stored for later use. Contractors can also store and sell ePatch mixes to third party agencies when hot mix is unavailable.
Mobile pugmills offer contractors the ability to mix the exact amount of material needed for a job, making on-site processing and application easy for larger leveling jobs. This is one of the top reasons many agencies and contractors decide to use ePatch for patching and leveling projects in their districts.
When blended at a hot mix plant, ePatch emulsion is delivered at approximately 160°F, then heated and run through the plant at temperatures between 170°F and 180°F. It is mixed with a 78 aggregate or a blend of 78s and 89s (or 3/8" and 1/4”) for best results with approximately 5% emulsion per ton. The finished material is then loaded on trucks and delivered to a storage area where it is allowed to cool and then is available for use.
Long Shelf Life
Patches made with cutbacks or hot materials can have short shelf lives. The hot material must be used before it cools and hardens, or in the instance of a traditional cold mix, it must be used before the diluent evaporates. ePatch’s revolutionary emulsion allows the patching mix to remain malleable for up to a year in dry storage. This creates great flexibility for agencies combating potholes in the winter when fresh materials may be hard to come by. Repairs done with ePatch extend roadway life by at least 2-3 years, depending on application or distress level.
Quick and Easy Application
ePatch instantly improves the quality of the driving surface. Where a traditional patching mixture made with cutback asphalt remains tender until the solvent evaporates, the engineered emulsion in ePatch allows roads to be released to traffic immediately after compaction. The cold patch can be placed into a pothole in the driving surface or used as a leveling material on uneven surfaces. For small patches, a hand-held compactor will set the mixture and create a sturdy patch, making it a quick and effective, one-man application. For larger leveling patches, a pneumatic roller may be required for adequate compaction.
Cost Savings
ePatch is the economical remedy to maintaining safe and adequate road conditions. The end result looks just like traditional hot mix, at a fraction of the cost and often without the need for heavy equipment. It is currently marketed to agencies in the Southeast as a means to address immediate needs of roadways that will last until planning and budgeting allow for longer-term and more extensive roadway projects.