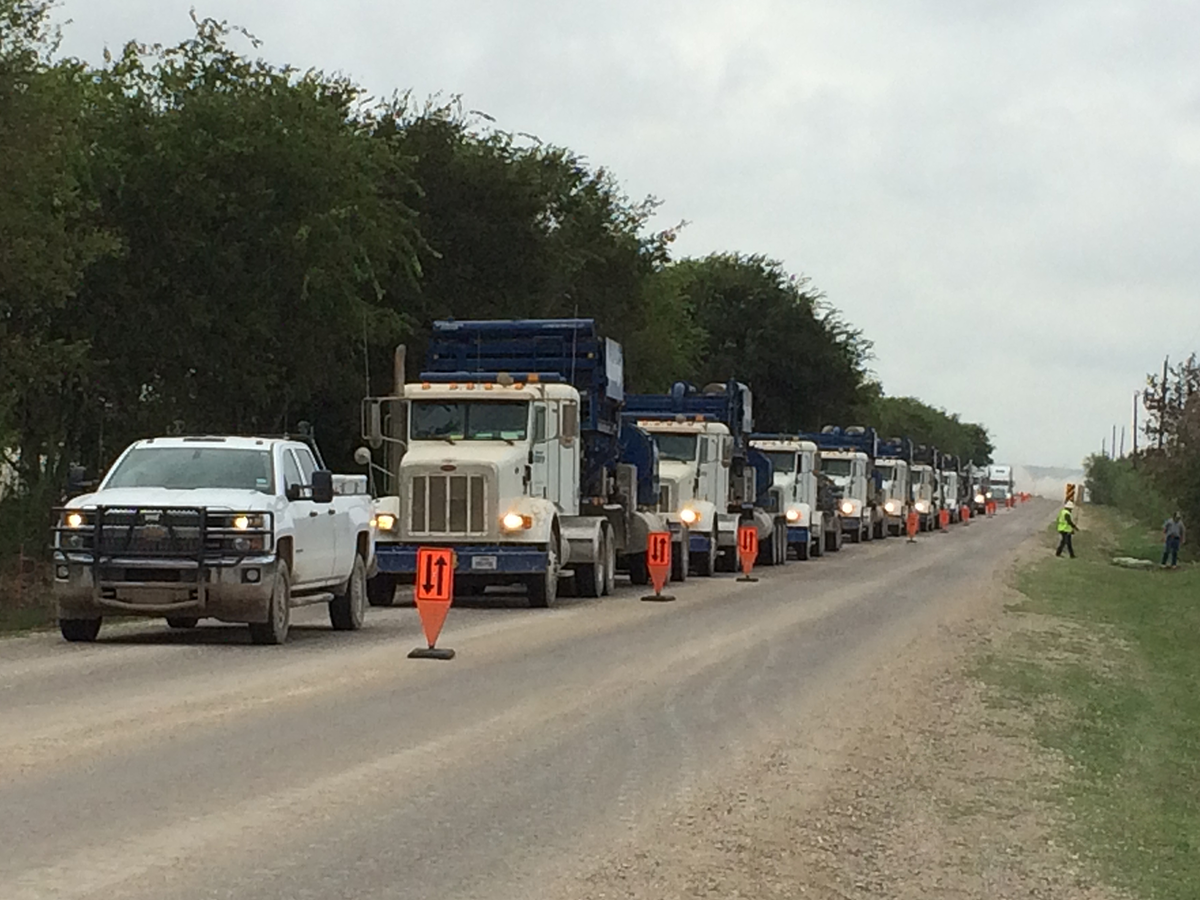
Typical heavy traffic loads on Watson Road in south San Antonio, TX.
Background
Watson Road, located in south San Antonio, Texas, (Bexar County) began to show cracking and ruts nearly six inches deep due to heavy traffic loads, poor drainage capabilities and a restricted outfall. The Bexar County maintenance crew graded ditches surrounding the road as much as possible, to allow excess water to flow from the pavement surface, but flat topography and lack of drainage easements prevented progress. This was becoming a continual maintenance headache for the county. With few options for alternative solutions, Bexar County Public Works Division Chief Tony Vasquez determined Full Depth Reclamation (FDR) would be the best solution to fully address moisture issues, restore and strengthen the road.
The process of FDR involves the recycling of a road’s existing wearing surface and base course mixed with a stabilizing agent. The mixture is then compacted to create a more durable road base and resistance to moisture damage. The stabilizing agent used in an FDR treatment depends on the severity of distress on the road receiving the treatment and can be either, or a combination of, asphalt emulsion, cement, lime or other chemical agents.
The county decided the asphalt emulsion CSS-1H, supplied by Ergon Asphalt & Emulsions, Inc., (Ergon A&E) was the best choice to meet the structural needs of Watson Road. This product consists of a hard form of base asphalt, and is a high quality, cost-effective solution specifically designed to promote strong bonds with existing road materials for a more resilient base course. The Texas Department of Transportation’s (TxDOT) specification for the FDR process requires a minimum unconfined compressive strength of 150psi (pounds per square inch) while a normal flexible base material only has to meet 45psi. The FDR treatment with asphalt emulsion would result in a much stronger base along with providing moisture resistance.
Application Highlights
The county construction crew used a Wirtgen reclaimer provided by Ramming Paving, Inc., to mix the 1.8-miles of Watson Road. The mix design provided by PaveTex Engineering and Testing called for an emulsion rate of 4.5% to meet agency specifications for strength. The emulsion was applied at a depth of 8 inches.
After mixing, the crew compacted the treated area using a vibratory padfoot roller followed by a maintainer or grader to level the surface. Additional compaction was achieved by using a pneumatic roller and finally a steel wheel roller in order to ensure an adequately shaped road able to withstand heavy traffic loads.
Full Depth Reclamation in progress. This treatment, with asphalt emulsion, results in a much stronger base and provides moisture resistance.
A Bump in the Road
Three days into application, the construction crew noticed 3"- 4" ruts on portions of the 0.9 miles of treated area. This was attributed to the emergence of unforeseen subsurface moisture brought to the surface by vibration from rollers during compaction. Halting operation, Ergon A&E’s Technical Marketing Manager Tom Flowers and Bexar County Assistant Superintendent John Jordan devised a plan to correct these ruts and address the subsurface moisture.
Adjust the Concept
Excess moisture present in the existing roadway during an FDR application usually calls for the addition of a drying agent in order to achieve proper moisture levels for a successful application. It is not uncommon for cement or lime to be used as drying agents in FDR projects in conjunction with asphalt emulsion. In fact, mixing too much water with emulsion can prove to be a deterrent to its performance.
The county decided to re-treat the rutted section of Watson Road at a depth of 3 – 4” with 2% cement, as well as an additional 1% of CSS-1H, which would actually correct the ruts and reform bonds that were broken in the process of re-mixing an already treated and compacted section. Without additional CSS-1H, the treated area would have still been vulnerable to moisture penetration whether cement was added or not, as its original design was disturbed. The addition of cement facilitated a drier surface, enabling the asphalt emulsion to provide optimum strength for the long haul.
The construction crew completed the remainder of the project course with 4.5% emulsion and 2% cement, the design adjusted to meet the new requirements of the roadway.
A two-course double chip seal surface treatment was applied to Watson Road following the FDR to protect the new base course.
The final product holding up well with no signs of rutting.
Stay the Course
The damage to Watson Road could have gotten much worse had the county not been proactive in finding a solution to 1) combat excess moisture and 2) steer the FDR treatment back on the right path mid-application. Furthermore, the decision to use asphalt emulsion as the main component in the FDR application, over cement, lime and other stabilizing agents, proved the best choice as it is the only solution designed to provide long-term strength and durability while also providing moisture resistance for the treated base.
Long-Term Strategy
Watson Road is now holding up well with a stronger road base and has not shown any signs of rutting. The county expects the FDR will meet expectations of serving as a long-lasting solution, extending the service life of this road for years to come.